Safety and Health Considerations for Fire Systems Professionals
At a recent fire industry technical conference, a group of attendees was asked why they entered this profession. The typical response was consistent with the industry’s universally recognized vision and goals: “To protect people and property.” While this is a noble and aspirational response, many attendees were not prepared for the next question: “What are you doing to protect your own employees?”
The archived 1923 news article from the Oregon Safety Council, Labor Bureau, and Industrial Accident Commission describes a fatal accident where a sprinkler fitter helper fell 32 feet from a scaffold to his death. This artifact is one of the earliest accounts of a workplace accident involving fire sprinkler contractors, and should beg the question, has the industry improved over the last 98 years? The passage of the Occupational Safety and Health Administration (OSHA) Act in 1970 and subsequent regulatory promulgations provide a minimum standard of protection for all workers in the U.S. However, unfortunately, approximately 5,000 workers still lose their lives every year in this country (USC 91-596, 1970).
Accident Statistics in the Specialty Trades
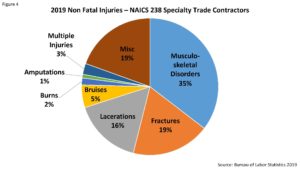
Another disturbing reality is that fatal accidents have been increasing over the last five years, while other types of injuries and illnesses have plateaued (BLS, 2020b). The fire systems industry is not immune to these events. Fire systems contractors can and have been injured and killed in the course of their work. Even as recent as 2020, an employee of a sprinkler installation contractor was killed and another critically injured when performing a sprinkler installation using a 26-ft scissor lift. In this tragic case, both employees worked from the basket of the scissor lift, installing 21/2-in. sprinkler pipe overhead at the height of approximately 26-28 feet. They attempted to move the fully extended scissor lift over a surface with an uneven grade when the equipment toppled over, resulting in both employees falling and striking the concrete floor below. One employee was killed instantly, and the other was hospitalized with critical injuries (OSHA, 2021b).
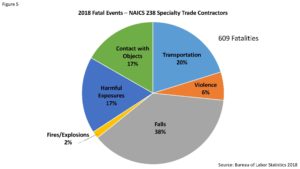
The most recent Bureau of Labor Statistics data for fatality events and non-fatal injuries for the North American Industrial Classification System (NAICS) for Construction: Specialty Trades Contractors includes the following types of fire systems contractors: fire sprinkler systems installation, fire alarm electric systems installation, waterless fire suppression systems installation and repair, security and fire systems installation, and fire-stop/fireproofing contractors. Research shows that, while overall fatalities, injuries, and illnesses are down over the last 12 years, the Specialty Trades Contractors (NAICS 238) subset continues to experience higher incident rates than the construction industry as a whole. Figures 1 and 2 show the highest type of events that occur in NAICS 238. Musculoskeletal disorders (38 percent), fractures (19 percent), and miscellaneous (19 percent) injuries are the most common types of non-fatal injuries. In comparison, falls (38 percent), transportation (20 percent), harmful exposures (17 percent), and contact with objects (7 percent) represent the most significant source of fatalities (BLS, 2020a).
What are the Most Common Risks in Fire Systems Installation and Maintenance?
Transportation In all industrial sectors, motor vehicle crashes are the number one cause of worker death. The National Safety Council reports that since 2015, all motor vehicle fatalities have increased year over year, primarily due to distracted driving. The U.S. has seen three straight years of at least 40,000 roadway deaths—from 2016 through 2018. Nevertheless, the risks of transportation accidents, specifically distracted driving, do not just apply to workers but others on the road that employees may encounter. A driver using a cell phone is four times more likely to crash when using a cell phone while driving, including during hands-free use. Commercial drivers who cause crashes where a cell phone is involved expose the company to significant liability. Employers were held liable for up to $25 million for employee-caused crashes (NSC, 2021). Furthermore, according to the National Council on Compensation Insurance (NCCI), non-fatal injuries sustained at work in a motor vehicle crash are the most costly, averaging $78,466 per claim (NSC, 2018).
Working at Heights While vehicle crashes are the top cause of death in all industries, falls are the number one cause of construction fatalities. In 2020, 167 deaths by falling occurred in the specialty trades sector (BLS, 2020b). The majority of these tragic events occurred when the employee worked from a ladder, scaffold, scissor, or aerial lift and was not protected by a proper fall prevention or arrest system. OSHA regulations require that workers exposed to a fall greater than six feet for construction, or four feet for general industry, be provided with some level of fall protection, dependent on the conditions of the work environment. Personal fall arrest systems include a body harness with a lanyard and one anchor point per person capable of withstanding 5,000 lbs of dead weight (OSHAb, 2020). Falls from motorized equipment such as aerial or scissor lifts are especially problematic because not only must the equipment be maintained in good working order, but employees must also be competent to operate the equipment properly to avoid toppling over.
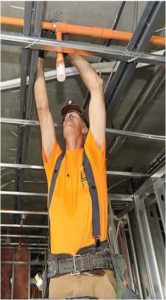
Human Factors and Ergonomics Musculoskeletal disorders (MSDs) account for 35 percent of all injuries in the specialty trades arena and account for over 400,000 injuries every year in all industries (BLS, 2020a). While these types of injuries are not typically fatal, they can cause life-altering body dysfunction for the workers who suffer them, and they can be tremendously expensive in terms of medical treatment and lost time away from work. The total costs of MSDs due to work-related are estimated to be between $45-54 billion annually. For example, the average shoulder injury requiring surgery and rehabilitation can cost upwards of $46,000, while a knee injury can cost an average of $33,000, and a lumbar (back) injury can cost anywhere between $40,000-$80,000 (NSC, 2018).
Another example of an MSD with high potential in the fire systems industry is thoracic outlet syndrome (TOS), a disorder occurring when blood vessels or nerves in the space between the collarbone and first rib (thoracic outlet) are compressed. This condition can cause pain in the shoulders and neck and numbness in the fingers. Common causes of TOS include physical trauma or injuries, pregnancy, or sleeping with arms above head. A concerning and work-related cause of TOS is repetitive overhead work such as that conducted by sprinkler system and fireproofing installers. Treatment for TOS usually involves physical therapy and pain relief measures, and surgery in extreme cases. Thoracic outlet syndrome that goes untreated for years can cause permanent neurological damage. The average cost of thoracic outlet surgery is $65,000 in direct medical costs, not including lost wages from being off work, physical therapy, and other associated indirect costs. Thoracic outlet syndrome prevention measures include maintaining good posture, joint stability and flexibility, and maintaining healthy weight and fitness levels (Mayo Clinic, 2019).
Rotating Equipment Working around unguarded rotating equipment can result in severe injuries, including lacerations, fractures, and amputation. In 2017, a pipe fitter lost two fingers when he was operating a threading machine. His right hand was in contact with the product as it spun on the machine and came into contact with the cutting blade, amputating two fingers. Furthermore, another tragic case was reported where a pipefitter was threading a pipe when his clothing became caught in the machine, twisting his shirt around his neck and suffocating him to death. The American National Standards Institute (ANSI) standard for pipe tools, B208.1-1982 paragraph 4.4 states that cord-connected portable pipe threading machines and portable power drives must be equipped with momentary contact devices such as a guarded foot pedal to control the power input to the portable pipe threading machine or power drive (ANSI B208.1, 1982). Furthermore, OSHA has issued a Hazard Information Bulletin for specific models of pipe threading machines not equipped with a dead-man footswitch that was involved in a fatal accident (OSHA, 1992).
Excavation and Trenching While it might not seem obvious that excavation hazards are prevalent to fire systems contractors, there have been a surprising number of incidents. Water supply tanks and piping that must be run underground can present a hazardous environment during site preparation and installation. Excavation and trenching are considered high-risk activities because when a trench collapses with workers inside, it almost always results in a fatality due to the sheer weight of soil and the time needed for rescuers to respond and initiate recovery safely. In 2012, A 40-year-old sprinkler fitter died when he was struck by and pinned against the wall of excavation by a water tank that had pivoted due to an excavation wall collapse (NIOSH, 2013). Safe excavation operations can be a complicated process that requires a very specialized knowledge set. The type of protective system used is specific to each configuration and soil type. In some instances, a registered professional engineer must design the protective system. A competent person must inspect excavations daily and be authorized to take corrective measures when appropriate, and employees who work in and around excavations must be trained (1926 Subpart P, 2020).
Electrical Contact and Arc Flash In addition to typical electrical hazards of fixed and portable powered equipment commonly found on a construction site, the risk of arc-flash concerning fire pump installation and testing is cause for concern. When operating a fire pump controller during inspection and testing, there is potential for an electrical fault and arc-flash whenever the switch is operated. NPFA 70E®, Standard for Electrical Safety in the Workplace®, requires hazard assessment and electrical equipment labeling to communicate the arc-flash energy potential, the minimum approach distances, and the necessary personal protective equipment that must be used. OSHA Lockout/Tagout regulations (29CFR1910.147), NFPA 70E, and NFPA 25, Standard for the Inspection, Testing, and Maintenance of Water-Based Fire Protection Systems, require that equipment be de-energized before maintenance to avoid unnecessary contact. However, NFPA 20, Standard for the Installation of Stationary Pumps for Fire Protection, requires a continuous power source, overcurrent reliability protection, and procedural protocols to avoid nuisance tripping (Holub et al., 2013). These standards may conflict in certain applications and should be reconciled with the Authority Having Jurisdiction (AHJ), the property owner, and the inspection, testing, and maintenance providers to ensure employees are protected.
Health Hazards A variety of chemical exposures can occur in sprinkler installation projects, from specialty chemicals used in the process to chemicals used by other trade contractors on the site. OSHA’s Hazard Communication Standard requires that chemical safety data sheets (SDS) be readily available to employees for every chemical they are exposed to, and training on protective methods must be provided.
Other health hazards that may be present include high noise levels from tools and equipment use, temperature extremes, both cold and heat, and sun exposure which can cause skin cancer. Sprinkler installers can be exposed to silica during concrete drilling or cutting concrete, especially when using rotary hammer tools and installing ceiling anchors. Sanding dry-wall mud and coring operations can be another source of exposure. Secondary silica exposures could occur while installers work in proximity to other trades such as masons, concrete work, demolition, and similar activities (Agnew, 2018).
In 2004, a mortality study of Canadian pipe trades workers (including sprinkler fitters) found a significant increase in esophageal, lung, and lymphatic cancers linked to exposures to asbestos, welding fumes, and other contaminants. The potential occupational exposures of pipe trade workers include the following known or suspected carcinogens such as acrylonitrile (lung, bowel); arsenic (lung, skin); asbestos (lung, pleural and peritoneal cavity, gastrointestinal tract); benzene (leukemia); beryllium (lung, bone); cadmium (lung, prostate); chromium (larynx, nasal cavity); nickel (nasal cavity, lung); styrene-butadiene rubber (lymphatic system); tar (scrotum, skin); and vinyl chloride (liver, brain, lung). Asbestos exposures still occur in buildings built before 1970, which can be prevalent during maintenance or retrofits (Finkelstein, 2004).
OSHA Regulations Apply to Fire Systems Contractors
In addition to the unacceptable proposition of injuries or fatalities, fire systems contractors are subject to OSHA enforcement inspections and possible citations and fines for safety and health violations. Penalties for violations can range between $13,653 per violation up to $136,532 per violation, depending upon the severity and circumstances. In 2015, the U.S. federal government enacted a law to adjust penalties for all regulatory agencies. This new law enabled OSHA to make a one-time 38-percent increase in fines and then adjust the penalties annually based on the Consumer Price Index (OSHA, 2021a).
Good Safety is Good Business
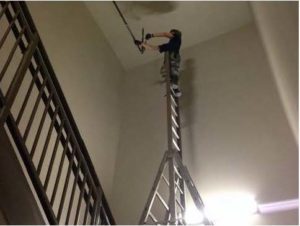
Safety practitioners, researchers, and even regulatory bodies have long identified a strong connection between low worker injury rates and an organization’s development of an organized and structured safety management system. Even OSHA confirms through their Voluntary Protection Programs that companies who invest in their workforce by implementing effective safety management practices see benefits, not only in reduced occurrences of accidents, but also in improved productivity, higher employee morale, lower turnover, and increased overall business profit, both in terms of reduced insurance, costs, but also in increased efficiency, effectiveness, and lower operating costs. A robust safety management system includes written policies and procedures and a strong culture of safety that pervades the mindset of supervisors and workers. The critical components of a robust safety management system include the following: leadership commitment to safety demonstrated both in the written word and actual practices in the field, employee engagement in the safety system, which includes the essential “Stop Work Authority” for high-risk situations, but also a climate where employees feel committed to safety, and the leadership team supports them. An integral component of a safety system is identifying and controlling hazards and risks through worksite analysis. This effort is ongoing, especially in the ever-changing environment of construction, and includes procedures, processes, and resources to address hazards in a timely fashion. Employee and Supervisory Training is another critical component of the system. Each person in the organization needs to be trained on the safety functions of their job, from fall protection to excavations and electrical safety. Supervisors and leaders need to be educated to understand their role and responsibility in protecting their crews from harm.
Construction activities are unique from other types of industries because they are dynamic and typically have multiple trades working alongside each other at any given time. Even if your employees are not directly exposed to a hazard, you may still be held responsible under OSHA’s multi-employer worksite policy. Finally, any program must be evaluated and improved over time.
Now That We Know the Risks, What Do We Do?
The myriad of safety and health concerns, including those described herein, can be overwhelming, especially for small contractors (OSHA, 2016). Consultation assistance is provided free in every state by the state OSHA Consultation programs. Workers’ compensation insurance carriers also typically provide safety and health assistance, and some even offer premium discounts for companies with strong safety and health programs.
Fire systems engineering, installation, inspection, and maintenance is an honorable business. The direct output of our efforts protects countless lives and saves billions of dollars every year for the clients we serve. Our mission is to protect the lives and property, including those occupants of the buildings we serve, the general public, and our noble fire service brothers and sisters. If this is true, then certainly one of our most cherished values should also be to protect our own employees’ lives and well-being.
WORKPLACE SAFETY RESOURCES
For more information on workplace safety, explore these additional resources:
Occupational Safety and Health Administration, U.S. Department of Labor – OSHA consultation services for small businesses. www.osha.gov/consultation
Bureau of Labor Statistics – Injuries, Illnesses, and Fatalities databases. www.bls.gov/iif
Center for Construction Research and Training – Safety and Health Network. safeconstructionnetwork.org
American Fire Sprinkler Association Safety Portal – www.afsasafetyportal.com
REFERENCES:
Agnew, R. J. (2018). OSHA’s Silica in Construction Standard Concerns for Fire Sprinkler Installers. Sprinkler Age, 37(1), 44–46.
ANSI B208.1. (1982). Portable Pipe Threading Machines and Portable Power Drives, Safety Requirement. In American National Standards Institute.
BLS. (2020a). Survey of Occupational Injuries and Illnesses 2019.
BLS, U. (2020b). Census of Fatal Occupational Injuries 2019.
Finkelstein, M. M. (2004). A cohort study of mortality among Ontario pipe trades workers. Occupational and Environmental Medicine, 61(9). https://oem.bmj.com/content/61/9/736
Holub, R. A., Doan, D. R., & Anderson, R. L. (2013). The arc-flash hazards of fire pumps: Redesigning protection schemes for electrical installations. IEEE Industry Applications Magazine, 19(1).
Mayo Clinic. (2019, September 12). Thoracic Outlet Syndrome. Diseases and Symptoms. https://www.mayoclinic.org/diseases-conditions
NIOSH. (2013). Pipefitter Dies When Excavation Wall Collapses, Causing Water Tank to Rotate and Pin Him Against Excavation Wall. https://www.cdc.gov/niosh/face/stateface/mi/12MI121.html
NSC. (2018). Accident Facts. https://injuryfacts.nsc.org/work/costs/workers-compensation-costs
NSC. (2021). Safety on the Road. National Safety Council. https://www.nsc.org/road
OSHA. (1992). Hazard Information Bulletin – Rigid Pipe Threading Machines.
OSHA. (2016). Recommended Practices for Safety and Health Programs (No. 3885). https:/www.osha.gov/safety-management
29 CFR 1926 Subpart M Fall Protection, Pub. L. No. 40 USC 3701, 29 CFR 1926 Safety and Health Regulations for Construction (2020).
29 CFR 1926 Subpart P Excavations, Pub. L. No. 40 USC 333, 29 CFR 1926 Health and Safety Standards for Construction (2020).
OSHA. (2021a, January 13). OSHA Penalties. Federal Register.
USC 91-596, Pub. L. No. 84 STAT.1590, Public Law 91-596 (1970).
OSHA, O. C. A. O. (2021b). OSHA Inspection 1464422.015.
ABOUT THE AUTHOR: Leslie Rex Stockel, MS, CSP, SMS, is an assistant professor of professional practice at Oklahoma State University (OSU) in Fire Protection & Safety Engineering Technology as well as instructional director for the OSU OSHA Education Center. Additionally, she serves as vice president of the board of directors for the Board of Certified Safety Professionals. Stockel earned a Master of Science degree in Engineering Technology Management, and a Bachelor of Science degree in Fire Protection and Safety Engineering Technology from OSU. She is currently pursuing her doctoral degree from Texas Tech University in Technical Communication and Rhetoric with an emphasis on Risk Communication. Stockel holds the Certified Safety Professional (CSP) and Safety Management Specialist (SMS) designations with the Board of Certified Safety Professionals. She has over 30 years of experience in the Safety and Health profession, working in both public and private sector organizations. Stockel can be reached via email at Leslie.stockel@okstate.edu.