Considerations of Mass Reopening
As the country moves toward reopening businesses and ending lockdown periods undertaken to help reduce the spread of COVID-19, everyone is focused on safety from an exposure standpoint. However, it is important to ask what impact these efforts have on fire protection and life safety? As workers strive to find new and creative ways to achieve social distancing, it’s unlikely that fire protection is at the top of their to-do list. Most business owners and facility operators are not focused on fire protection and life safety as they seek to find ways to safely reopen and protect their employees from virus exposure. Efforts to protect both their employees and the general public could have negative impacts on fire protection and life safety. Those professionals performing fire protection system maintenance and inspection are the most likely population to identify and inform of such issues. It’s important for contractors, inspectors, and enforcement authorities to be aware and on the lookout for these issues and help businesses correct them.
What do inspectors, installers, and consultants need to be aware of in this changed environment?
Sprinkler Systems and Social Distancing
Essential businesses have been taking efforts to increase the distance between customer-facing employees and the customers they serve. In some cases, these businesses are creating physical barriers. A common example is a plexiglass barrier at customer service desks with small openings through which employees can exchange materials with a customer, where six feet of physical distance is not practical. However, erecting any physical barriers that act as walls could negatively impact the fire protection system. Sprinklers are spaced within a facility to ensure that a specific density of water is delivered that will be adequate to control a fire based on the hazard classification of the expected fuel load. When physical barriers are erected that could block part of a sprinkler’s spray pattern, there may be areas that will not receive any of the water delivered from the closest sprinkler. As a result, the fire would continue to grow unchecked for a longer period of time before sprinklers around it are activated. Not only would the sprinkler system be unable to potentially reach the seat of a fire, but this extended period of fire growth could result in a fire that is much larger—it is possible that the design density of the sprinkler system would be inadequate.
Before erecting full- or partial-height barriers, facility owners should engage a fire protection professional to evaluate any impact on sprinkler spacing. It may be necessary to add additional sprinklers to ensure that full-height barriers do not create a sprinkler system impairment. Alternatively, partial-height barriers that don’t extend all the way to the ceiling may provide an opportunity to limit exposure between employees and customers without impacting sprinkler coverage. In any case, it will be necessary for someone experienced with the obstruction requirements in NFPA 13, Standard for the Installation of Sprinkler Systems, to determine how high a barrier can extend before it creates a sprinkler impairment.
Those conducting routine sprinkler inspections and maintenance need to be aware of this potential issue and look for temporary or permanent barriers that may have been erected in an effort to maximize social distancing. Where new barriers have been added, the sprinkler spacing must be evaluated to ensure that the minimum required level of protection can still be achieved without sprinkler system modifications.
In offices with open floor plans and cubicle layouts, social distancing can be challenging. In some cases, employees may take it upon themselves to modify their office furniture to limit their exposures in the office. One of the ways people could do this includes adding a top on full-height cubicles or building barriers around desks and cubicles.
Material used to create vertical barriers around desks and cubicles not only impacts the sprinkler system coverage, but there may also be a higher hazard fuel load. Using foam core board, expanded polystyrene foams, plastics, or glue-based laminated wood products may not meet the combustibility requirements for furnishings. Plastics, untreated laminated wood products, and foams often have much higher heat release rates during a fire than the ordinary combustibles most office sprinkler systems are designed to protect. As a result, large quantities of such materials could increase the fire load to a point where a fire could overwhelm the sprinkler system.
Smoke Control
Some facilities with office areas that open to atriums or other vertical spaces may have smoke control systems to help maintain tenability long enough to evacuate occupants during an emergency. When products like plastics and foams are added in significant quantities the smoke production may be greater than that for which the smoke evacuation systems were designed to handle. As a result, the available safe egress time could be reduced in the event of a fire.
Fire inspectors need to be aware of the impact that fuel loading could have on such systems like sprinkler systems and smoke exhaust systems and ensure that efforts to reduce physical exposure aren’t reducing the level of protection in the facility.
Egress
As people return to work, many businesses may find it difficult or impossible to maintain social distancing with current desk and floor plans. They may seek to rearrange furniture and office layouts to increase physical separation. However, in undertaking such efforts, owners and facility operators should employ a fire protection professional to review floor plan changes prior to implementing them. Reduced aisle widths, blocked exits, increases in egress travel distances, common paths of travel, and dead ends could hamper evacuation in the event of an emergency. It is important that such changes are reviewed to ensure that the minimum code-prescribed level of protection is maintained with proposed arrangements. In addition, where floor plan changes are employed to maximize social distancing efforts, any required occupant egress plans would need to be updated to reflect those changes.
Exit Enclosures
Another life-safety challenge that is occurring as a result of social distancing efforts has to do with exit stairwells. In some cases, to reduce the need for people to potentially touch surfaces such as doorknobs, some buildings are leaving stair doors propped open for circulation from floor to floor. However, stairs in these buildings are required fire-rated exit enclosures and the door is an integral part of that required fire-resistance rating. Additionally, in high-rise buildings, exit stairs may be pressurized to prevent smoke from a fire from infiltrating the stairwell so that occupants have a safe and tenable exit route. When doors are propped open these stairwells act as chimneys to allow smoke to freely travel from floor to floor, and occupants may be exposed to untenable environments in smoke contaminated exits. Smoke-filled exit stars have been major contributing factors in fire deaths in many large-loss fires in the U.S. Stair pressurization systems are designed to compensate for a number of stair doors to be opened for egress activities but propping open all the stair doors is very likely to render the pressurization system incapable of maintaining positive pressure. In addition, if the stair door is propped open on the fire floor, the stair has a high likelihood of quickly spreading dangerous smoke and products of combustion not only to the exit enclosure but to other floors with doors that are propped open. A better approach is to provide tissues or paper towels outside the stairs for occupants to use to protect their hands from contacting the door opening hardware and then providing trashcans outside the stair enclosures on each floor for disposing of the paper products.
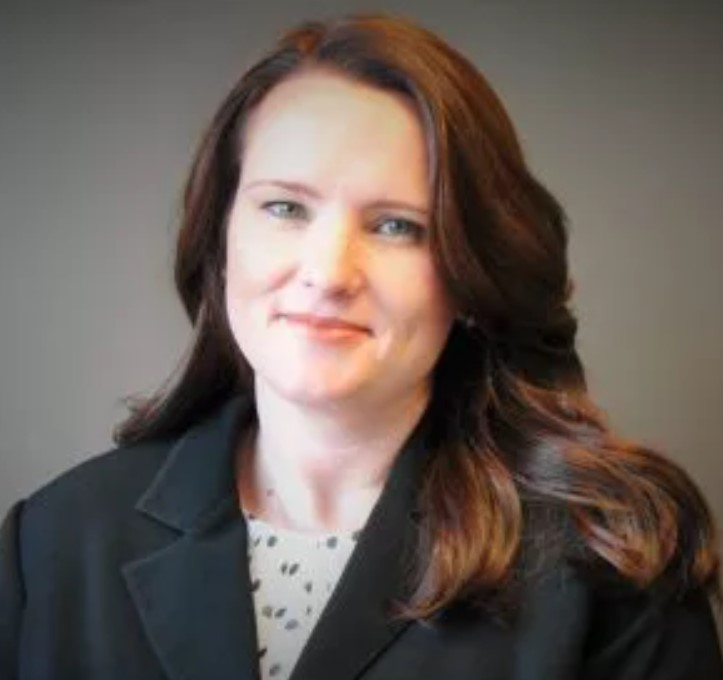
ABOUT THE AUTHOR: April Musser, P.E., MBA, is Southeast regional practice leader of fire protection engineering for Telgian Engineering & Consulting (TEC). She has more than 15 years of experience in fire protection engineering and consulting, including code consulting and design. Musser has designed fire- and life-safety systems for large commercial and industrial facilities and has managed projects across a wide range of market segments across the Southeast and internationally. She has also presented at numerous well-known conferences including the NFPA Annual Meeting and Conference, SFPE Southeast Annual Fire Safety Conference, Georgia Fire Safety Symposium, and the Campus Fire Safety & Emergency Management Conference. Musser is the author of numerous articles on building fires and their impact on fire and building codes for a wide variety of industry publications. Visit Telgian.com.