Protection for a Mobile Power Generation Unit
Summary Jackson Associates, Inc. was approached by a government contractor to analyze protection of a power generating unit (PGU) which is part of a large trailer unit. The trailer is built to fit inside a large military aircraft for rapid deployment throughout the world. The unit was being designed and tested by a consortium of military manufacturers and contractors.
Jackson Associates, Inc. was assigned the portion of the project intended to explore potential types of extinguishing systems to protect the power generating unit for the program and identify the strengths and weaknesses of the various systems. We do not have permission to provide any photographs or information regarding the purpose of the units.
Project Task The PGU module contains two diesel generators. The main fire hazard would be from a diesel fuel leak that could cause a pool fire or an atomized spray fire. The design parameters call for storage in a range from -40°F to 150°F and operating temperatures of 35°F to 125°F Because of the extreme congestion inside the PGU most systems would require locating the extinguishing storage vessels on the exterior of the PGU. The weight of the system is also a significant factor for air transportation. The lower extremes in temperature obviously eliminate any water-based extinguishants, without some type of freeze protection. The PGU also requires many openings to allow for cooling during operation. We chose to look at the following extinguishing systems:
1. Clean Agent Systems
A. INERGEN
B. ECARO-25
C. NOVEC-1230
D. FM-200
2. Carbon Dioxide
3. Compressed Air Foam
4. Dry Chemical
5. Aerosol
6. Water Mist
We were unable to find an approved antifreeze presently available for water mist systems (although there is speculation that it may be in development). Therefore, water mist was eliminated from consideration. The following is a description of the qualities of the remaining five types of systems.
Clean Agent Systems “Clean agent fire extinguishing system” is a term that covers a wide variety of extinguishants which were developed as alternative replacements for Halon 1301 and other halons. The Montreal protocol of 1987 imposed severe international restrictions on production of halons, freons and other chlorofluorocarbons (CFCs) that were detrimental to the earth’s atmosphere. Design and installation of clean agent extinguishing systems are governed by NFPA 2001. The most common halon replacements are:
1. Inergen (IG-541) N₂(52%) Ar(40%) CO₂(8%)
2. ECARO-25 (HFC-125) CF₃ CF₂H
3. NOVEC-1230 (FK-5-1-12) CF₃CF₂C(O)CF(CF₃)₂
4. FM-200 (HFC-227ea) CF₃ CHFCF₃
Each of these will be described below.
Inergen Inergen utilizes inert gasses and works by lowering oxygen levels below the level that will allow combustion while at the same time maintaining an oxygen level that would allow humans to continue to occupy the space. In this application, Inergen has three main drawbacks:
1. It requires maintaining a very accurate concentration level. In this application, with high ventilation rates and unclosable openings, this will be impractical.
2. The amount of gas is significant and is stored in heavy high pressure cylinders that would add undesirable weight.
3. The refill stations are tightly controlled by the manufacturer, which greatly reduces availability for recharge after a discharge.
Because of these three drawbacks, Inergen was eliminated from consideration.
ECARO-25, NOVEC-1230 and FM-200 All of the above clean agents have an ozone depletion potential (ODP) of zero. Both FM-200 and ECARO-25 have a significant global warming potential (GWP), whereas NOVEC-1230 and Inergen have a GWP of 1. This makes NOVEC-1230 and Inergen preferable as extinguishing agents, from an environmental standpoint, since all four agents have similar extinguishing capabilities. Since Inergen was eliminated, as explained above, we consider Novec-1230 as the preferable clean agent.
A white paper by Mark L. Robin, PhD, of DuPont, which provides technical details of the various chemicals, can be found at www.chemours.com/FF/en_us/assets/downloads/pdf/K22197_role_of_HFCs_whitepaper.pdf.
The following are advantages of clean agents and specifically of NOVEC-1230:
1. NOVEC-1230 is very effective and will quickly extinguish the fire without an adverse effect on personnel in the area.
2. The system size and weight is reasonable.
3. The equipment is durable.
4. Since NOVEC-1230 is a liquid at normal room temperature, for recharging it is easily transferred to the cylinder which is then pressurized with nitrogen.
5. There is no clean up and the generator can be restarted immediately.
6. NOVEC-1230 is environmentally friendly.
7. It is not corrosive to electronics.
8. NOVEC-1230 systems are UL listed and FM approved.
Disadvantages of NOVEC-1230 are:
1. Industry standards are that an extinguishing concentration is to be maintained for 10 minutes. The system is required to discharge in no more than 10 seconds. However, the unclosable openings in the PGU make it likely that the extinguishing concentration will be maintained for less than one minute. Due to the heat from the diesels, re-ignition of the fire is a real concern once the gas concentration descends below the required level.
2. NOVEC-1230 can absorb moisture if not properly handled during recharge, causing it to become acidic. Acidity can cause reduced effectiveness and cause corrosion of the cylinder.
3. Clean agents function by chemically reacting with the fire and interfering with the fire chemical reaction. In order to do this, the clean agent breaks down into other chemicals when heated to extreme temperatures at the flame. The broken down chemicals can be toxic. In order to minimize the toxic chemicals, clean agents are required to discharge totally in a maximum of 10 seconds. When the system discharges it could create a potential concern. The discharge would extinguish the fire but, after the NOVEC-1230 leaks out the unclosable openings, the lower concentration could allow the fire to restart. With the inadequate concentration, the fire could produce excessive amounts of toxic gasses from the breakdown of the clean agent. One of the reasons that clean agents are typically required to maintain extinguishing concentration for a minimum of 10 minutes is to assure that the fire cannot restart, creating toxic chemicals from the extinguishing agent.
4. Because of the size, the cylinder and actuator would need to be located in a weather-tight enclosure on the outside of the PGU.
Carbon Dioxide Carbon dioxide has been successfully utilized for fire suppression for more than 100 years. The NFPA standard for carbon dioxide is NFPA 12, Standard on Carbon Dioxide Extinguishing Systems. Carbon dioxide displaces oxygen to a percentage that will not support combustion. Following a discharge, the oxygen percentage is also below the level that would be necessary to support human life. Because of this safety issue, NFPA 12 now prohibits the use of carbon dioxide in occupiable areas (areas where it is possible for a person to enter) without several safety features. To install carbon dioxide in occupiable areas, various safety requirements are required, including:
1. Safety signs at all entrances.
2. An electrically monitored lock-out valve.
3. A pneumatic (CO₂-powered) pre-discharge siren.
4. Pneumatic time delay.
5. Audible/visual discharge alarm signals at each entrance to indicate that the system has discharged.
6. A distinctive and recognizable odor that must be added to the carbon dioxide. This is typically accomplished with a wintergreen odorizer provided by the equipment manufacturer.
The above safety devices add complexity and expense to the system.
The following are advantages of carbon dioxide systems:
1. It is very effective and will quickly extinguish the fire.
2. Carbon dioxide is an oxygen diluting agent and does not break down like clean agents. Therefore, the code allows it to take up to 2 minutes to achieve the design concentration. Because of this, we can easily extend the discharge and maintain the concentration with extra gas for several minutes.
3. The equipment is durable.
4. Carbon dioxide is readily available around the world.
5. There is no clean up and the generator can be restarted immediately.
6. Carbon dioxide is a greenhouse gas, but the quantities are negligible.
7. It is non-corrosive to electronics.
8. Carbon dioxide systems are UL listed and FM approved.
Disadvantages are:
1. It displaces oxygen so it is hazardous and potentially lethal to personnel inside the PGU.
2. In order to address safety concerns, additional safety equipment is required.
3. There is significant expense in training all personnel on the precautions and procedures for safety.
4. The carbon dioxide is stored in high pressure cylinders that are bulky and heavy.
5. Because of the size, the cylinder and actuator would need to be located in a weather-tight enclosure outside of the PGU.
Compressed Air Foam Compressed air foam is a hybrid type foam system that incorporates a foam tank filled with a freeze-protected, premixed foam water solution. To discharge the foam, a compressed air tank pressurizes the tank and forces the solution into a mixing chamber. There, air is mixed with the solution, causing it to expand between 10 and 20 times and then flow through piping to discharge nozzles. It has been used extensively in portable extinguishing systems at military airports and in large engine compartments. The following are advantages of compressed air foam:
1. The foam is very effective at extinguishing both pool fires and three dimensional fires.
2. The foam will blanket the burning liquid and remain effective for an extended period.
3. The systems are fairly compact.
4. The equipment is durable.
5. Recharge is simple. Just pour in the new foam solution and refill the air cylinder.
6. The foam is widely available.
7. The foam is environmentally friendly.
8. The discharge nozzles are standard open sprinklers.
9. The foam is not corrosive to electronics although drying out any exposed electrical components could be necessary.
10. The foam solution is UL approved.
Disadvantages are:
1. Clean-up may require vacuuming out the foam and drying out the PGU.
2. While it is non-corrosive, it is an aqueous solution and any critical exposed electrical is a concern.
3. There are no nationally recognized listings of the units as fixed systems.
Dry Chemical Dry chemical is one of the most widely used fire extinguishants. It is most commonly used in portable fire extinguishers. However, it is also available in larger industrial and vehicular systems. NFPA 17, Standard for Dry Chemical Extinguishing Systems, governs the installation of dry chemical systems. Dry chemical systems utilize a chemical powder which chemically reacts and interrupts the fire chain reaction.
The following are advantages of dry chemical:
1. It can effectively extinguish a fire and could continue to remain effective for several minutes.
2. The system size and weight are reasonable.
3. The equipment is durable.
4. Recharge is very simple, involving loading the powder and pressurizing with nitrogen.
5. The chemical is widely available.
6. It is environmentally friendly.
7. UL listed and FM approved.
Disadvantages are:
1. The systems are extremely messy (envision throwing 50 pounds of powdered sugar in the air).
2. The clean-up inside the PGU would be extensive.
3. Dry chemical can be corrosive to electronics and aluminum if not properly cleaned up. For example, dry chemical should not be used around aircraft because of potential damage. See the related Boeing Service letter at http://arffwg.org/wp-content/uploads/2012/08/sl-737-03-004.pdf.
4. Personnel must be trained. While there would probably be no lasting effects, if personnel were inside the PGU when it discharged, inhalation of the dry powder and/or getting it in the eyes would be very unpleasant.
5. Because of the size, the dry chemical cylinder and actuator would need to be located in a weather-tight enclosure outside of the PGU.
Aerosol Aerosol fire suppression systems are a relatively new fire suppression product, in comparison to many of the other products. NFPA 2010, which was first issued in 2005, governs the design and installation of aerosol fire extinguishing systems. Systems are available that can operate automatically at a preset temperature, manually, or electrically from a listed fire alarm releasing panel.
The sealed aerosol generators, through an exothermic reaction, discharge extremely small aerosol particles between 2 and 10 microns. Because of the small size of the particles, they suspend in the air and will remain suspended for an extended amount of time in the enclosure. Since the particles are suspended in air, when the generator cooling air is stopped the aerosol particles are less prone to leaking out of enclosure openings than most gaseous extinguishing agents that are heavier than air.
The following are advantages of aerosol:
1. Much smaller and lighter than other extinguishing systems. A single generator could be located inside the generator enclosure (the size of a large coffee can) that would weigh around 20 pounds. All other systems would need to be in weatherproof enclosures outside the PGU and would weigh many times 20 pounds.
2. The aerosol can effectively extinguish a fire and can remain effective for an extended period – often up to an hour.
3. Sealed generators require much less maintenance than the remotely mounted agent containers of other systems.
4. The equipment is very durable.
5. There is no piping into the PGU that could require removal for servicing of the PGU.
6. It is fairly economical to install a second generator as reserve in order to provide continued protection to restart the generator after a fire.
7. The enclosure is not pressurized, as it would be with discharging of gaseous systems. Therefore, the extinguishant is not ‘pushed’ out of the PGU during discharge.
8. The aerosol generators are sealed units so there is no recharging. The generator is simply replaced with a new unit.
9. The aerosol particles are not corrosive to electronics.
10. Cleanup is very minimal.
11. Generators are UL listed.
Disadvantages are:
1. If discharged while personnel are working in the PGU, there could be temporary eye irritation.
2. The gasses discharging out of the unit can be up to 100°C, but temperatures decrease rapidly as you get away from the generator.
3. The units were tested by Underwriters Laboratories to a maximum of 130°F so the generators are listed for 130°F. The manufacturer stated that they typically will function well above that and have been extensively used in military vehicles in Afghanistan.
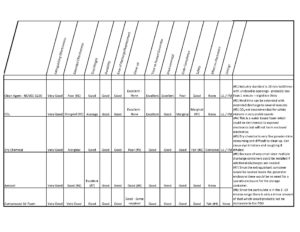
Conclusion With the design requirement for this application, it became apparent that aerosol was the best fit. Some of the favorable factors were the compact equipment, lightweight, no piping, limited clean up and lack of corrosiveness to aircraft aluminum. Figure 1 below compares the various sytems analyzed for this project.
ABOUT THE AUTHOR: Rick Jackson graduated from Wittenberg University in 1974 with a bachelor’s degree in engineering science/physics. He has worked in the HPR department at Kemper Insurance and at a special hazards company. In 1979, Jackson Associates, Inc. was incorporated, and designs and installs all types of special hazard and sprinkler systems. Jackson is a member of AFSA, NFPA’s Industrial Section, and SFPE. He has served on NFPA 409 Aircraft Hangar and NFPA 750 Water Mist committees, Michigan SFPE board of directors, and AFSA’s Technical Advisory Committee. Call 248-762-2500 or email rick@jacksonassociatesinc.com to contact him.